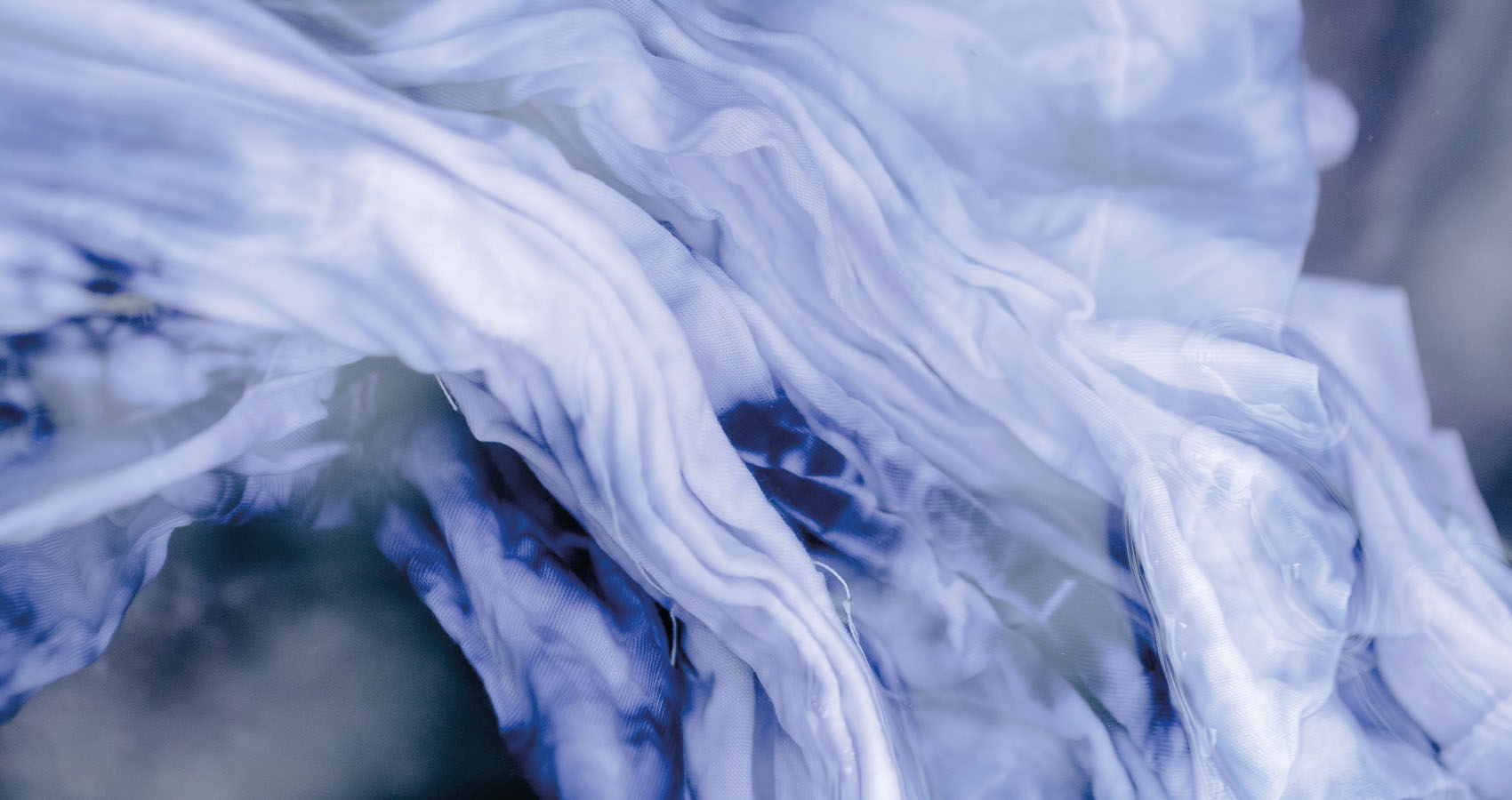
What Our Jeans Aren’t Telling Us: Part Two
Denim deceit? We think not.
If you read ‘What Our Jeans Aren’t Telling Us: Part One,’ you will hopefully be more familiar with the cotton production process and how we can look out for these tell-tale signs as consumers on the shop floor. But unfortunately, cotton cultivation is not the only water-intensive process in creating denim. The traditional dyeing process, which denim typically endures, is unsustainable as it discharges a vast amount of wastewater and uses immense energy supplies and chemical products.
Dry Indigo Technology
Compared to the traditional denim dyeing process known as slasher dyeing (or sheet dyeing), dry indigo dyeing cuts down on chemical usage and energy consumption and eliminates almost 100% of wastewater, as the foam application process does not require water usage. The technique was developed from 10 years of research conducted by Gaston Foam Systems and Indigo Mills Design and was exclusively carried out at Tejidos Royo- a Spanish denim mill.
So, not only does using dry indigo technology in the dyeing process of denim reduce the water quantity needed in the production of denim jeans, but the process also cuts out 89% of the chemical products that are needed in other dyeing methods. A smaller space is also used during this resourceful technique so that energy usage can be lessened by up to 65%. This would be revolutionary if the mass fashion market adopted this technique as a dyeing method. The solutions exist, but they need to be built into the model of mass denim production. Banana Republic was one of the first brands to pilot the technology, but they did not standardize the practice in their business model. Keep your eyes peeled for dry indigo dyeing processes, as this will become a significant future player in fashion.
Up Next, How Modern Celebrity Culture Is Promoting Consumerism More Than Ever