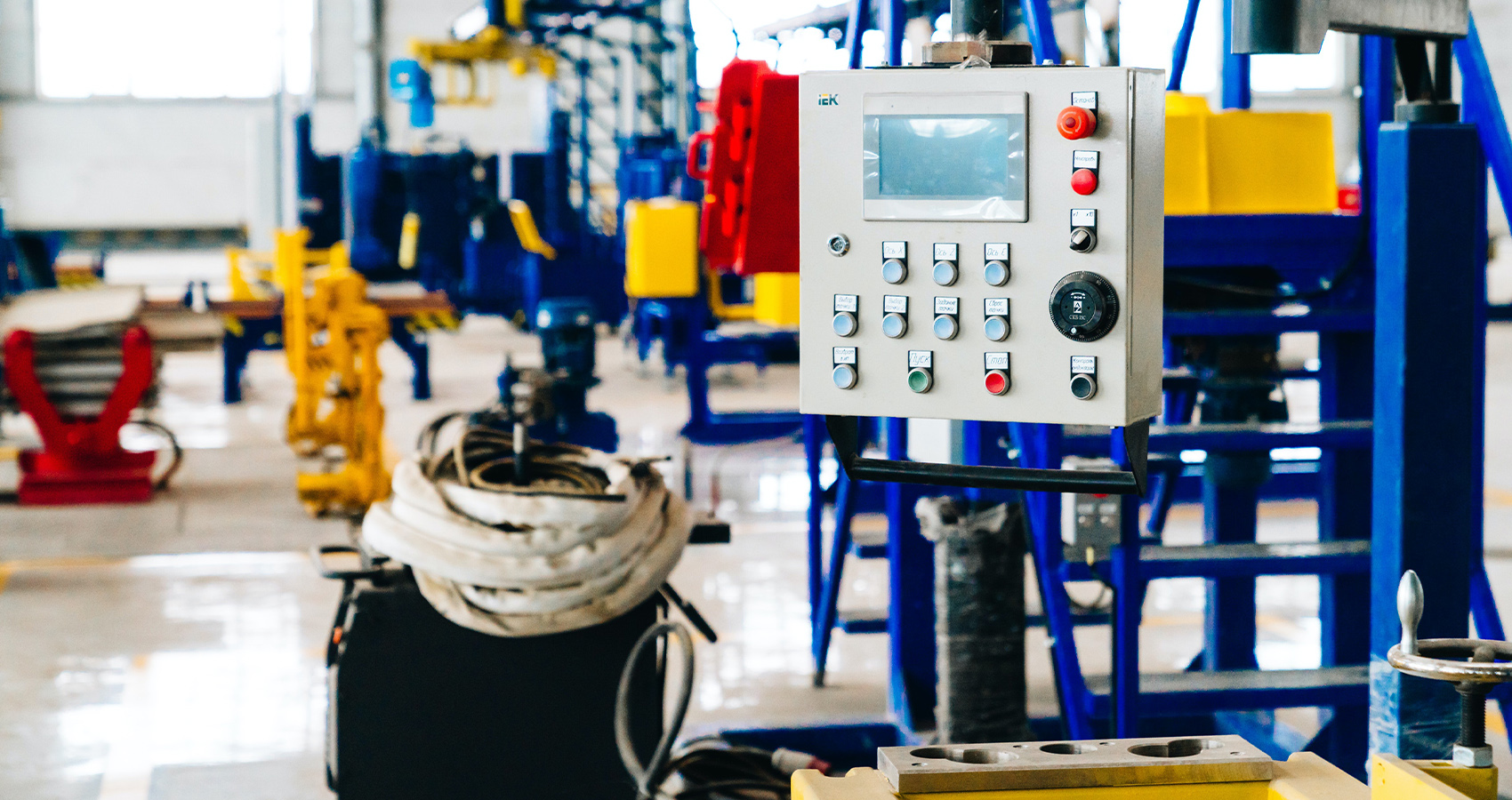
The Pros and Cons of a Pneumatic Conveying System
A method of transporting materials like powder, dry bulk and granules for processing in plants.
Pneumatic conveying is a method of transporting materials like powder, dry bulk and granules for processing in plants. These materials are transported via an enclosed pipeline. A force of pressure usually through a gas flow of air is applied to move the materials to their destination.
The system includes a motive source of air usually referred to as an air mover. This can be a blower or a fan. It also includes a feeder or loader to introduce the material into the system. Additionally, it includes the conveying line, a termination receptacle or material receiver and a system to collect dust.
A lot of materials could be pneumatically conveyed as long as they are fairly dry. Examples of these are flour, plastic pellets, sand, cement and hundreds of food products, chemicals and minerals. Materials in the form of paste or slurry are not suitable to be conveyed pneumatically.
There are two categories of a pneumatic conveying system and these are dilute phase and dense phase. You can read about conveyors systems from this article.
How A Pneumatic System Works
Doing any kind of work requires a form of energy. This is also true for a pneumatic conveying system. Energy is required to transport materials through the system. However, in this situation, the energy is supplied via a pressure differential which is in pounds per square inch. In addition to this, there is an airflow that is measured in cubic feet per minute.
The air pressure present in the conveying line in a pneumatic system is changed by an air mover. This air mover either generates pressure or a vacuum. Whatever is generated is dependent on where this air mover is located in the system.
If it is located at the start, the air mover will push air through the system making it operate under pressure. If located at the end, the air mover pulls air through the system instead making it run under a vacuum. The system will successfully transport materials when the pressure or vacuum, as well as airflow within it are controlled.
Advantages Over A Mechanical Conveying System
Typically a mechanical conveying system runs on a straight line and with minimum directional changes. Each of its directional changes will require its drive and motor. The system is also mostly opened rather than closed making it susceptible to generating dust. It also requires frequent maintenance due to many moving parts.
Additionally, mechanical systems take up lots of valuable space. On the other hand, some of the advantages of a pneumatic conveying system is that it is easy to install, maintain as well as operate. It uses a simple and small diameter pipeline for transferring materials.
This pipeline can be arranged in a way to fit in with existing equipment. This provides it with a flexible layout and uses less space. This system is completely enclosed and has few moving parts thereby requiring little maintenance. It also means that this reduces concerns of dust, contamination and air quality.
Disadvantages When Compared To A Mechanical Conveying System
A pneumatic system typically uses more horsepower and consequently more energy to operate than an equivalent mechanical system. The main reason for this is that changing the air pressure consumes a huge amount of power. In this regard, it is less efficient than a mechanical system.
This kind of conveying system requires a much larger dust collection system than the mechanical one. The reason for this is because it has to separate the transported material from the transporting air at the end.
Furthermore, pneumatic conveying systems are best suited for bulk and dry materials. Other kinds of materials may be difficult to transport within the system. Examples of these include those with large particle sizes as well as high bulk density like rocks and gravel.
Slurry, sticky and materials in paste form may also not be transported using a pneumatic conveying system. They are easier to transfer using a mechanical one that is designed to handle them.
Applications of Pneumatic Conveying Systems
Some common ways to use this kind of conveying system include:
Feed lance injection in steelmaking as well as in non-ferrous metal smelting.
Recycling
Burner feeding using alternative fuels and combustible dust in cement industries.
Used in friable products like in carbon black prills and pet food post-extruders.
How To Select A Pneumatic Conveying System
The first thing to consider in choosing a pneumatic system is the property of the materials to be transported. This talks about the size, shape, moisture content, bulk density, friability and the abrasiveness of the material. It also includes its static charge, hygroscopicity, toxicity, melt point, explosivity, etc.
Secondly, you need to consider how the system can fit into your plant environment or your location. These include the length and planned routing. There should also be a consideration for easy access to components and during maintenance.
Thirdly, you should consider the rate at which the system must transport materials to meet your expectations. You can check out https://www.sttsystems.com/systems/pneumatic-conveying/ if you require more information about all these.
Conclusion
Pneumatic conveying comes with both advantages and disadvantages when compared to mechanical systems. Nevertheless, it provides the best method for transporting some materials.
If the materials you have to work with are mostly dry, powdery and heavy bulk, you will do well to use this system. It is easy to install and maintain as well as flexible.